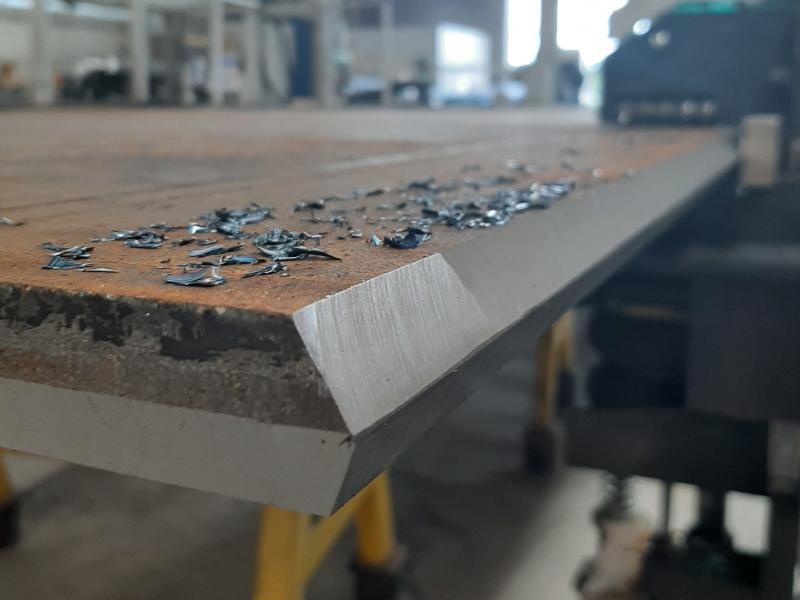
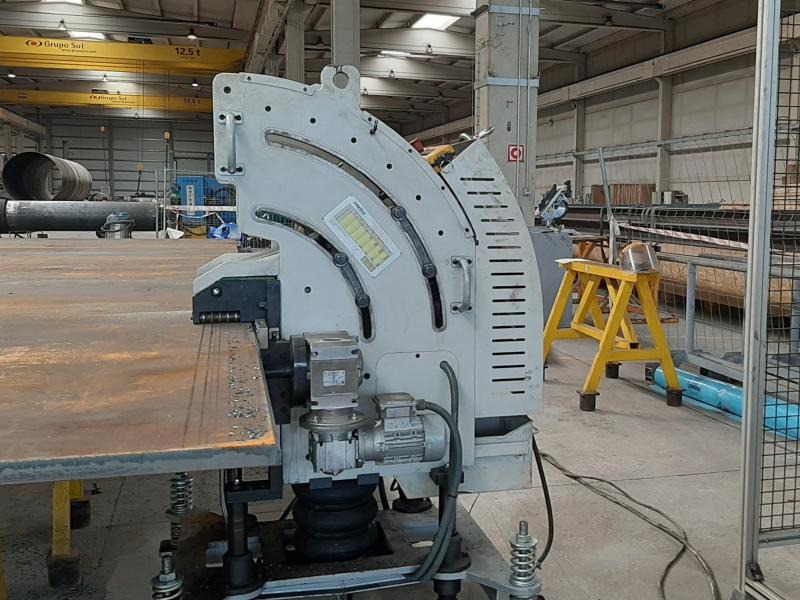

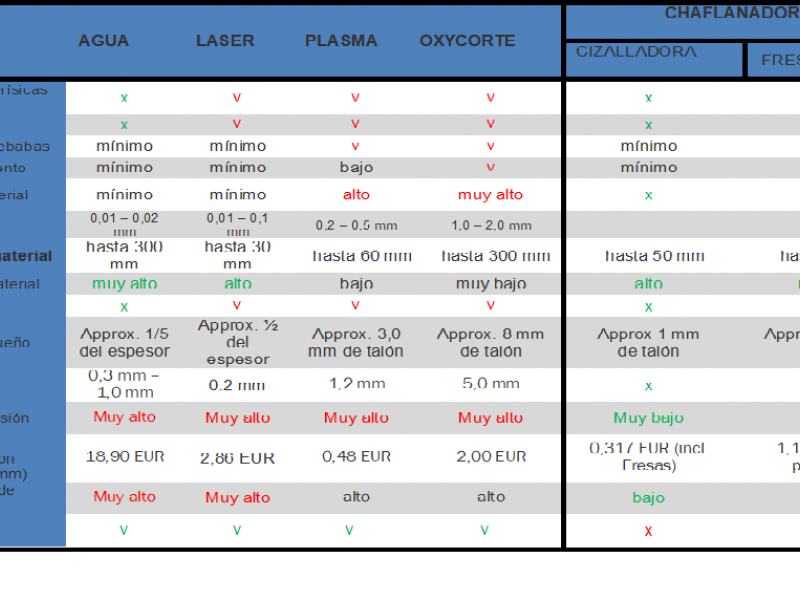
Laser, water or plasma cutting? An investment-intensive CNC system that takes up a lot of space? The mechanical processing of bevels is extremely useful in many cases and is of interest and attention to many users. 3D contour chamfers are not always required. Many users often face the question of which chamfering method is the most economical for their application, since the advantages of the chamfering method come into play depending on the requirements and the material. However, these processes are not in competition with each other, but form a meaningful alliance in many manufacturing processes.
We will explain the most common chamfering methods below.
• Mechanical chamfering
• laser cutting
• Water jet cutting
• Plasma cutting
• Overview
Mechanical chamfering with welding edge milling and chamfering machines with roller shears
In addition to the efficient and professional results, a major advantage of mechanized weld preparation is the health-friendly way of working. In contrast to the common methods of preparing weld seams, which produce fine dust or even toxic gases that get into the ambient air and can thus be inhaled, mechanized processing only results in chamfer sections, milling chips, nibble lumps or coarse chips that simply fall on the floor or in the designated containers.
To ensure the best possible connection quality at the weld seam, oils, greases, varnishes, paints and oxide layers on parts to be welded must be removed so that the joint edges on which the work is carried out are metallically clean. When processing, you should also make sure that no oil-containing coolants and lubricants are used so that the preparatory work is not neglected. The mechanized weld preparation avoids this. With this procedure, we resign cooling water containing emulsions, which in most cases is used in the preparation of weld seams by manual methods or CNC milling machines, and instead mill, shear or grind the material completely dry.
Edge milling machines
Mobile bevelling machines are increasingly replacing the classic procedures for preparing weld seams, such as roller shears, burning and manually angle grinders. Modern, powerful machines not only ensure greater efficiency, they also impress with their high surface quality. The machine moves to the metal plates or work fix with smaller pieces, so its use is very flexible.
Edge processing with the shear method
The most efficient way of preparing weld seams is with the roller shear machines.
These bevelling machines operate using the roller shear method. Here, a long chip is sheared off the sheet edge by means of a slowly rotating cutting wheel or shear wheel. This enables speeds of up to 3 m / min (up to 5 times faster than conventional methods). The costs for the meter chamfer are up to 75% lower than with other processes! Without dust and without noise, since there are no milling chips and no grinding dust.
Advantages and disadvantages
Advantages
- Cutting all conductive materials
- Cutting thicknesses up to 100 mm
- Cutting high-alloy steels
- Low noise
- High profitability
- Optimal use of materials
- Narrow kerf width
- No thermal stress
- Cutting thick material
- Safer for users and the environment
- No post-processing required
- Low operating costs
- High cutting speed
- Short set-up times
- No specialized staff required
- Without large part restrictions
Disadvantages
- Rough end result for roller shears.
- High specialization, not applicable for other processes.
- Limited material thicknesses
Características del láser
The laser has opened up new applications in the field of sheet metal processing. In the thin sheet metal sector in particular, there is no way around laser cutting due to the high cutting speeds and low thermal stress. The laser processing impresses with almost rectangular cutting edges and a minimal cutting gap with achievable tolerances of up to +/- 0.1 mm / m. An almost unlimited variety of materials has made the laser number 1 among cutting tools in many areas. Stainless steel up to 50 mm, steel up to 40 mm and aluminum up to 20 mm can be cut safely. But lasers are also used for processing in other material groups such as wood, plastic or paper. The disadvantage of laser cutting is the reduced process stability with reflecting surfaces, a limited sheet thickness range and the extensive occupational safety measures.
Advantages and disadvantages
Advantages
- High cutting speeds
- No burrs
- Low heat influence
- Perfect dimensional accuracy
- Best material utilization
- Short processing times
- Minimal cutting gap
- Great variety of materials
Disadvantages
- High investment costs
- Limited material thicknesses
- Comprehensive occupational safety
- Process instability with reflections
Cutting with the water jet
Water jet cutting is an effective alternative to conventional cutting processes and the ideal cutting solution for many users. From foam to hard sapphire, with a high-pressure water jet of up to 6,200 bar, even the hardest materials become as soft as butter. Especially when it comes to heat-sensitive materials, this is an useful method. Thanks to the latest technological developments, this innovative process is entering new areas of accuracy and productivity. The result is a significantly improved quality of part tolerance and angular accuracy. The addition of sharp-edged abrasives such as sand or quartz can further increase the effectiveness of water jet cutting, which is why very thick material thicknesses can also be cut. Stainless steel up to 300 mm and aluminum up to a thickness of 400 mm can be cut.
Advantages and disadvantages
Advantages
- High profitability
- Great variety of materials
- Optimal use of materials
- Narrow kerf width
- No thermal stress
- Cutting thick material
- High precision down to the micro range
- Safer for users and the environment
- Often no post-processing is required
Disadvantages
- High operating costs
- Great risk of corrosion
- Slow cutting speed
- Treatment of the cutting water
- Disposal of the abrasives
Explanations of plasma cutting
Plasma cutting has made significant progress in recent years due to the development of state-of-the-art multi-gas burners and is one of the most economical separation processes, particularly for thick CrNi sheets and in the medium steel range. The cutting quality in the thickness range from 15 mm to 40 mm is the same as that of laser cutting. However, this thermal separation process impresses with high cutting speeds, which is why the productivity of the manufacturing process is significantly increased. Especially in the production of components that still have to be welded, turned, milled or further mechanically processed, plasma cutting offers extensive advantages.
Advantages and disadvantages
Advantages
- Cutting all conductive materials
- Cutting thicknesses up to 200 mm
- High quality in medium strengths
- Cutting high-alloy steels
Disadvantages
- High operating costs
- Relatively wide cutting gap
- Usually high noise level
- Hardening of the marginal zones
- Post processing required
Conclusion for comparison
What is the best cutting method?
There is no clear answer to this question, because first it has to be clarified what is meant by the term "best"? And depending on the cutting task, a certain method is most appropriate. No process can be considered the only correct one, but all cutting processes have their authorizations, their special areas of application, strengths and weaknesses, advantages and disadvantages and individual cost structures.
It always depends on the application.
What are your criteria for a good cut, for the best cut?
Is it the manufacturing cost of the blank?
Is it the accuracy of the cut parts according to ISO 9013?
Is it the thermal influence, the structural change in the material?
Is it the weldability of the blanks?
Is it the hardening of the material and thus its suitability for the ISO 1090 execution classes?
Does the quality of the material require certain treatment rules?
Is the geometry requirement on the cutting very high?
What does the post-treatment of the blank look like, should it be painted, powder coated or galvanized?
Etc.
The large number of criteria therefore makes it impossible to make blanket statements. Your customer's requirements and the economic efficiency of the bevel production are significant.
Laser cutting is always the first choice, particularly in the thin sheet sector, and impresses with its high level of economy. This allows workpieces from a wide variety of material groups to be manufactured with very high component accuracy without mechanical finishing.
For material thicknesses over 300 mm, only the torch and water jet cutting are suitable. With a look at the quality, a decision to cut water steel is certainly logical, but not all users can make this investment and do not have the necessary space.
If the aim is only to make the chamfering process profitable, the decision to use the mechanical chamfering process is obvious. The mechanical processes are gentle on health, economical and handy. Various solutions can be offered for sheet thicknesses from 3 mm to 100 mm. The finishing is very different. Chamfering on chamfering machines with roller shears is very precise with regard to the angular accuracy, but has a rough surface, which is caused by the action of the cutting wheel. However, this corrugated pattern is irrelevant for the subsequent welding process, since the material is completely melted during welding.
If the final processing requirement is high, the welding edge milling machine is a very good alternative. Even very resistant metals such as Hardox and Duplex can be processed and chamfers up to 60mm can be created.
The major disadvantage of the chamfering machines is their high degree of specialization, they cannot do anything else.