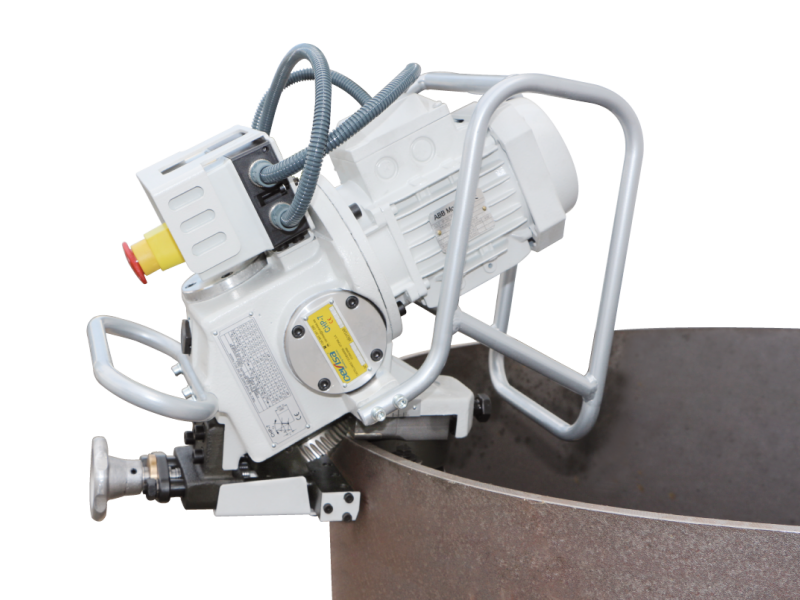
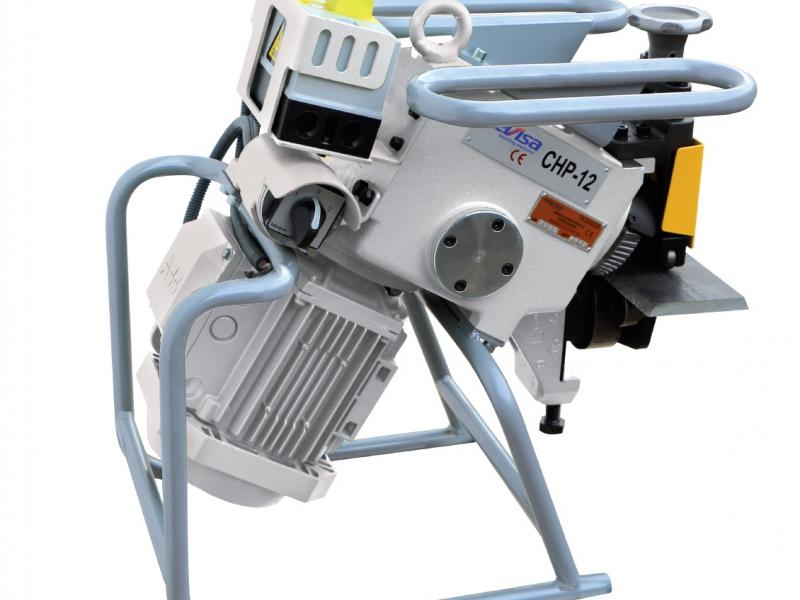
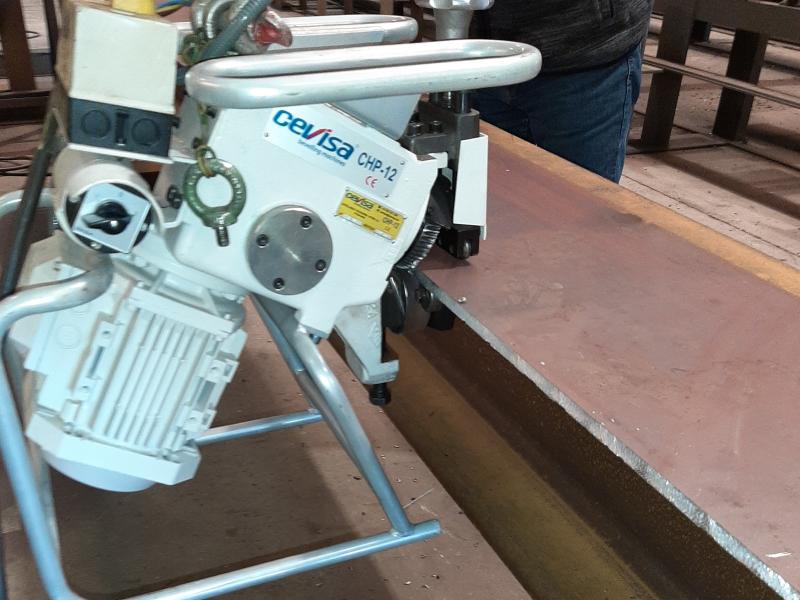
In metal manufacturing companies, chamfering is often one of the relevant processes that is not given enough importance. Undoubtedly, poor weld edge preparation is the first and most fundamental cause of improper adjustments resulting in poor quality welds due to inaccurate V-joint preparations. Excessive welding, increased heat input and increased expenditure on consumables and personnel as well as additional hours are the consequences. All of these factors contribute to lower productivity with additional costs that harm today's cost optimization requirements.
The importance of accurate weld preparation is easy to understand looking at a few sectors of heavy industry, such as shipbuilding or the manufacture of tubular wind energy towers.
The manufacturing of tubular windmill towers is not as complex as shipbuilding, but it relies on welding numerous sheets of metal with constant precision to produce the shells that form the tower, up to 100 m. This particular application requires chamfers of at least 1500 m in one day (three shifts) for a production level of “one tower per day”. In both of the above sectors there is a need to find a fast, precise, consistent and economical chamfering process with minimal or no heat input to enable good quality welds for carbon steels, high strength steels, stainless steels, aluminium and other alloy steels.
Process Selection: Choosing the most appropriate process can be complex as there are many factors to consider. There may be only a few options that are suitable for a particular application. However, the final choice will generally depend on the ability to economically manufacture the quality bezels required. These factors can include:
• Type of material.
• Range of sheet thicknesses to be bevelled.
• Required cut quality.
• Complexity of edge preparation.
• Precision of the cutting process.
• Number of sheets / tubes
• Permissible tolerances of the process.
The most common method of oxy-fuel cutting (chamfering) is used to cut carbon steel plates. Manual devices are inexpensive and can be used manually.
Disadvantages of using this method can be low speeds, high heat input, possible inaccuracies in the bevel angles and bevel surface (which leads to excessive weld seam deposition). It also creates significant costs for gases and other consumables, including the inevitable waste and manpower. When CNC flame cutting machines are used, the plates have to be fed into the machine and this implies the use of a crane which is an expensive and time-consuming operation, and we would no longer be talking about low investment equipment.
In return, CEVISA has bevel machines that work on the rotary shear principle and are very effective due to their portability and manoeuvrability at high bevel speeds of 1.7 to 2.6 m per minute. These bevellers can bevel plates with a thickness of 6 to 50 mm and offer precise and uniform weld seam preparation “V”, “K” or “X”. With these machines different materials like carbon steels, alloy steels, stainless steels, aluminium can be chamfered very successfully. Mechanical chamfering, which is not a thermal process, has the important metallurgical advantage of not creating a heat modified zone and causing no thermal distortions.
Other significant advantages of mechanical bevelling are:
1. Operation free from noise, pollution and vibration.
2. These machines are easily carried to work and are self-propelled and follow the edge of the panel while chamfering without operator assistance.
3. The suspension trolley enables the machine to be operated on uneven ground.
4. Quick and easy adjustment.
6. No special skills are required to operate these machines.
7. The top and bottom of the panels can be chamfered with two machines at the same time.
Inverted or rotatable bevel machines that are used simultaneously in conjunction with standard bevel machines can create a double V bevel without rotating the sheets. This saves crane time, processing time and repetition time, compresses the total throughput cycle time and increases productivity at optimized costs.
All of these factors undoubtedly make chamfering machines a preferred choice in the manufacturing industry to improve weld preparation and weld quality in the base and avoid high welding costs. Good welders are expensive and scarce, so it's consistent to recognize that consistency in quality and aesthetics are also of paramount importance.